The Rise of IoT-Enabled Smart Factories: Revolutionizing Industrial Production
In today’s fast-paced technological landscape, the advent of the Internet of Things (IoT) has brought about a paradigm shift in the way industries operate. One of the key areas where IoT is making a significant impact is in the realm of smart factories, also known as Industry 4.0. These smart factories utilize IoT technology to connect machinery, sensors, and devices to streamline and automate manufacturing processes, leading to increased efficiency, agility, and productivity.
Transformation of Traditional Factories:
Traditional factories have often been characterized by isolated systems, manual processes, and limited connectivity between machines. However, with the integration of IoT devices, these factories are evolving into smart manufacturing units that are interconnected, data-driven, and able to make real-time decisions. The ability to gather, analyze, and act upon data in an automated manner is revolutionizing industrial production.
Key Components of IoT-Enabled Smart Factories:
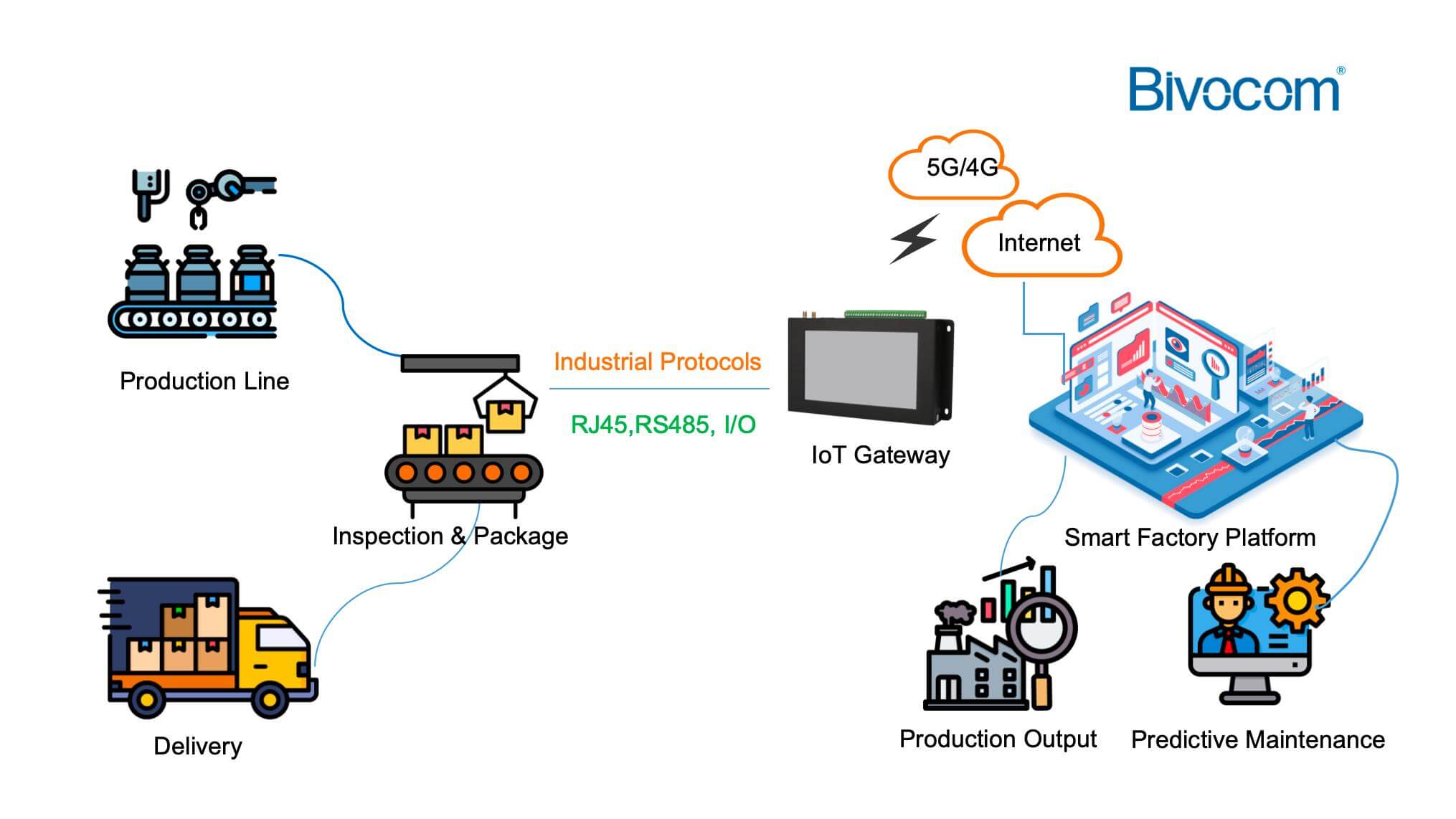
Icon source: https://www.flaticon.com/
- Sensors and Devices: IoT sensors embedded in machinery and equipment collect real-time data on performance, energy consumption, and maintenance needs. These sensors transmit data to a centralized system for analysis and decision-making.
- Connectivity: High-speed networks and communication protocols like Wi-Fi, Bluetooth, and 5G ensure seamless connectivity between devices within the factory ecosystem. This enables swift data exchange and coordination among machines.
- Data Analytics: Advanced analytics platforms process the vast amounts of data collected from sensors to derive valuable insights. Predictive maintenance, production optimization, and quality control are some of the areas where data analytics plays a crucial role.
- Automation and Robotics: IoT enables the integration of automation and robotics into manufacturing processes, leading to greater precision, speed, and safety. Robots can perform repetitive tasks with high accuracy, freeing up human workers for more strategic roles.
Benefits of IoT-Enabled Smart Factories:
- Increased Efficiency: IoT technology optimizes production processes, reduces downtime, and minimizes waste, leading to enhanced efficiency and cost savings.
- Improved Quality Control: Real-time monitoring and analysis of production data enable early detection of defects and deviations, ensuring higher product quality.
- Enhanced Flexibility: Smart factories are agile and adaptable to changing market demands. Production can be easily modified or scaled based on real-time insights.
- Worker Safety: IoT-enabled sensors can detect hazardous conditions in the factory environment, ensuring the safety of workers and preventing accidents.
Challenges and Considerations:
Despite its numerous benefits, the implementation of IoT in smart factories comes with challenges such as data security risks, interoperability issues, and the need for skilled workforce training. Companies must invest in robust cybersecurity measures, standardized protocols, and employee training to fully harness the potential of IoT in industrial settings.
In conclusion, IoT-enabled smart factories are reshaping the future of manufacturing by driving innovation, efficiency, and competitiveness. As technology continues to advance, the adoption of IoT in industrial settings will only accelerate, ushering in a new era of interconnected and intelligent production processes. The journey towards fully realizing the potential of Industry 4.0 is well underway, and the possibilities it holds for the manufacturing sector are truly transformative.
1 Comment