Bivocom 5G Gateway TG463 Revolutionizes Textile Industry
Introduction
The textile industry has been rapidly evolving, embracing advanced technologies to optimize production processes and meet the increasing demands of the market. In this era of Industry 4.0, the integration of IoT (Internet of Things) solutions has become pivotal in enhancing operational efficiency and driving productivity. Among these cutting-edge solutions, the Bivocom 5G Gateway TG463 has emerged as a game-changer, offering comprehensive features for energy management, production output optimization, machine status monitoring, and predictive maintenance in the textile sector.
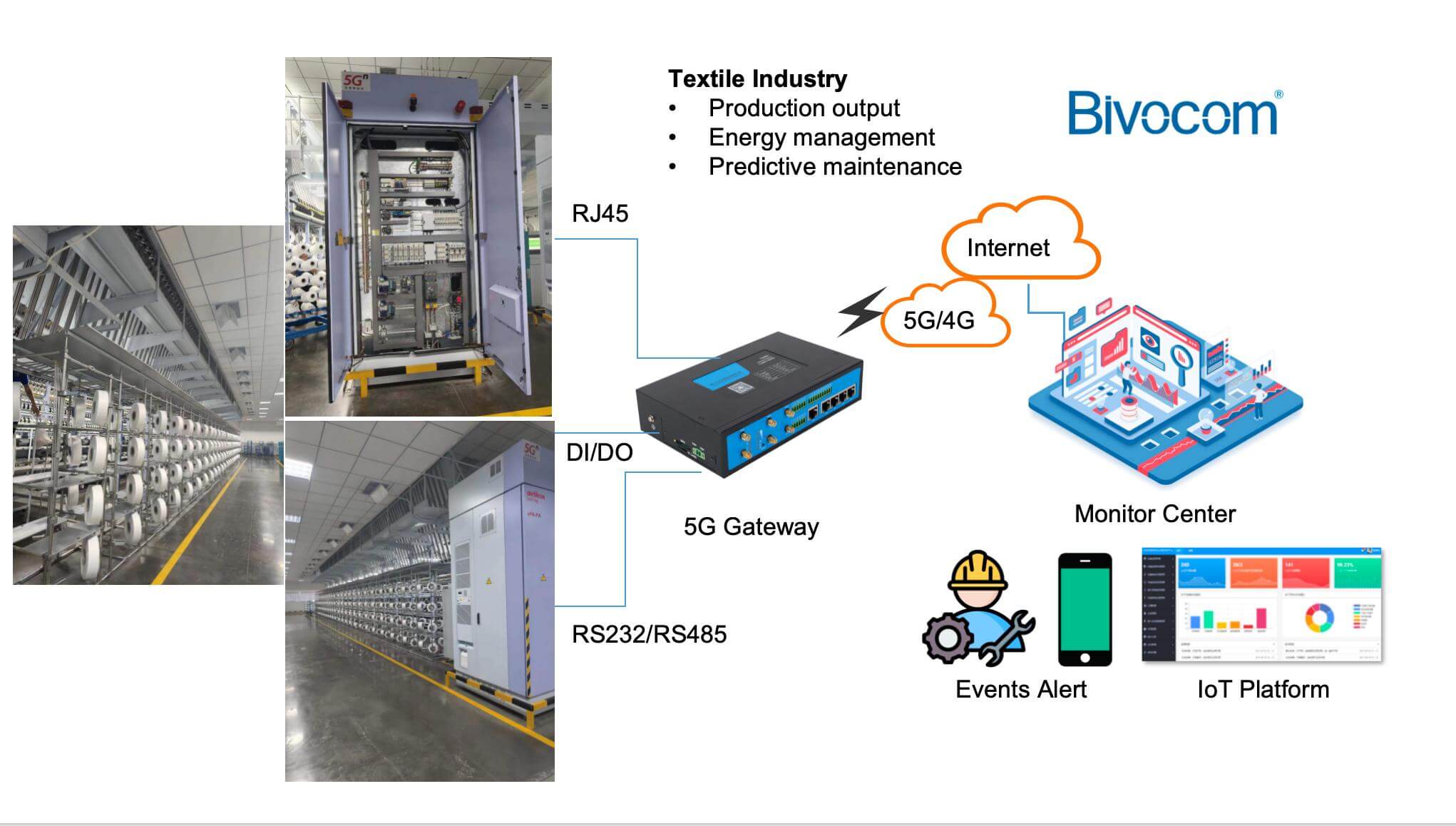
Revolutionizing Energy Management
Energy costs constitute a significant portion of the operational expenses in textile manufacturing. With the Bivocom 5G Gateway TG463, textile facilities can effectively monitor and manage energy consumption in real time. By integrating the gateway with smart sensors and meters, manufacturers can gain valuable insights into energy usage patterns, identify areas of inefficiency, and implement proactive measures to reduce energy waste. This not only leads to substantial cost savings but also aligns with sustainability initiatives, as textile companies strive to minimize their environmental footprint.
Optimizing Production Output
Maintaining consistent and high production output is crucial for textile manufacturers to meet market demands and stay competitive. The Bivocom 5G Gateway TG463 empowers businesses with real-time data analytics capabilities, enabling them to monitor production processes, identify bottlenecks, and streamline operations for enhanced productivity. By leveraging this technology, textile companies can proactively address production inefficiencies, minimize downtime, and ensure optimal utilization of resources, ultimately leading to improved output and higher customer satisfaction.
Enhanced Machine Status Monitoring
Textile manufacturing heavily relies on complex machinery and equipment. Any unexpected downtime or equipment failure can severely impact production schedules and profitability. By deploying the Bivocom 5G Gateway TG463, textile facilities can implement advanced monitoring systems that provide real-time insights into the operational status of machinery. Through predictive maintenance algorithms and remote diagnostics, manufacturers can preemptively address potential issues, schedule maintenance activities, and avoid costly unplanned downtime, ensuring smooth and uninterrupted production processes.
Empowering Predictive Maintenance
Traditional maintenance practices often lead to either over-maintenance, resulting in unnecessary spending, or under-maintenance, leading to equipment failures. The Bivocom 5G Gateway TG463 overcomes these challenges by enabling predictive maintenance strategies. By harnessing machine learning and AI algorithms, the gateway facilitates the analysis of equipment performance data, predicting maintenance needs with precision. This shift from reactive to proactive maintenance not only extends the lifespan of critical machinery but also optimizes maintenance schedules, reducing costs and enhancing operational reliability.
Conclusion
As the textile industry continues to embrace digital transformation, the Bivocom 5G Gateway TG463 stands out as a versatile and powerful IoT solution, offering a wide array of benefits for energy management, production optimization, machine status monitoring, and predictive maintenance. By harnessing the capabilities of this innovative technology, textile manufacturers can gain a competitive edge, drive operational excellence, and adapt to the dynamic landscape of Industry 4.0, while meeting the demands of a rapidly evolving market.
The integration of the Bivocom 5G Gateway TG463 represents a significant step forward in revolutionizing the textile industry, empowering businesses to stay ahead in a fast-paced and increasingly technology-driven environment.
Comment