Have you ever heard of Industry 4.0, and thought about how 5G and IoT technology will transform the future’s manufacturing and factories? This article will show you how 5G IoT empowers Industry 4.0, the new world of smart connected machines and intelligent robots.
Before we jumping to Industry 4.0, let’s take a look at the previous 3 industrial revolutions.
Industry 1.0
Key words: water power, steam power, mechanization
The first industrial revolution was started from 1760 to 1840 in England, when steam and water power was first used to create mechanical production facilities, and has helped us to move from hand to machine, and from farms to the first factories.
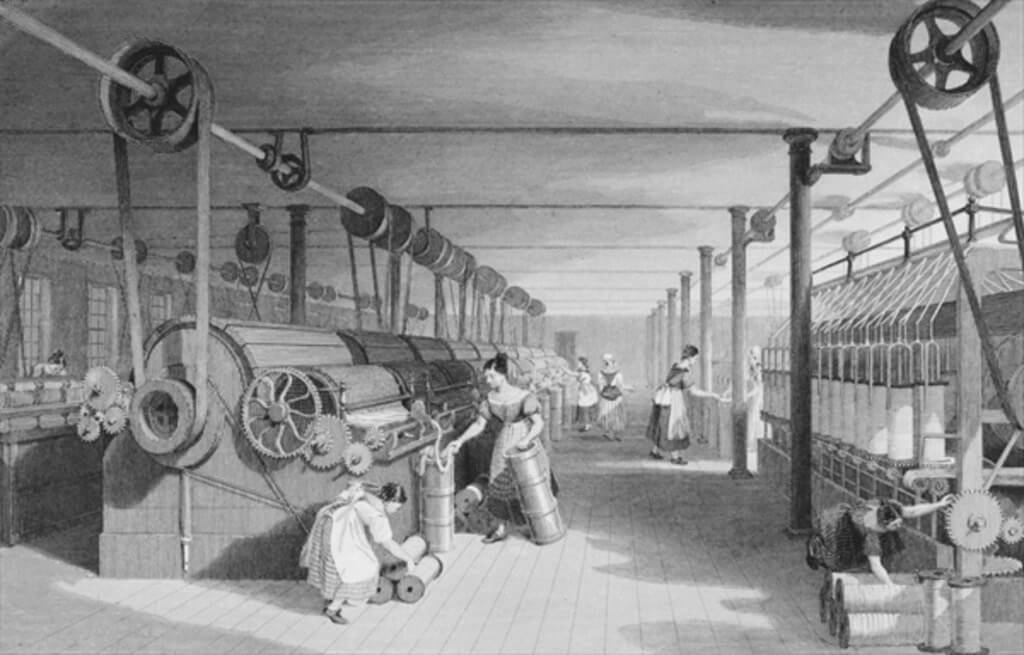
Image source: Medium
Industry 2.0
Key words: electricity, mass production, assembly lines
The second industrial revolution was started from 1870 to 1914, thanks to the electricity, the electricity gave us automation and assembly lines to create a division of labor and mass production, and this is the real start of factories.
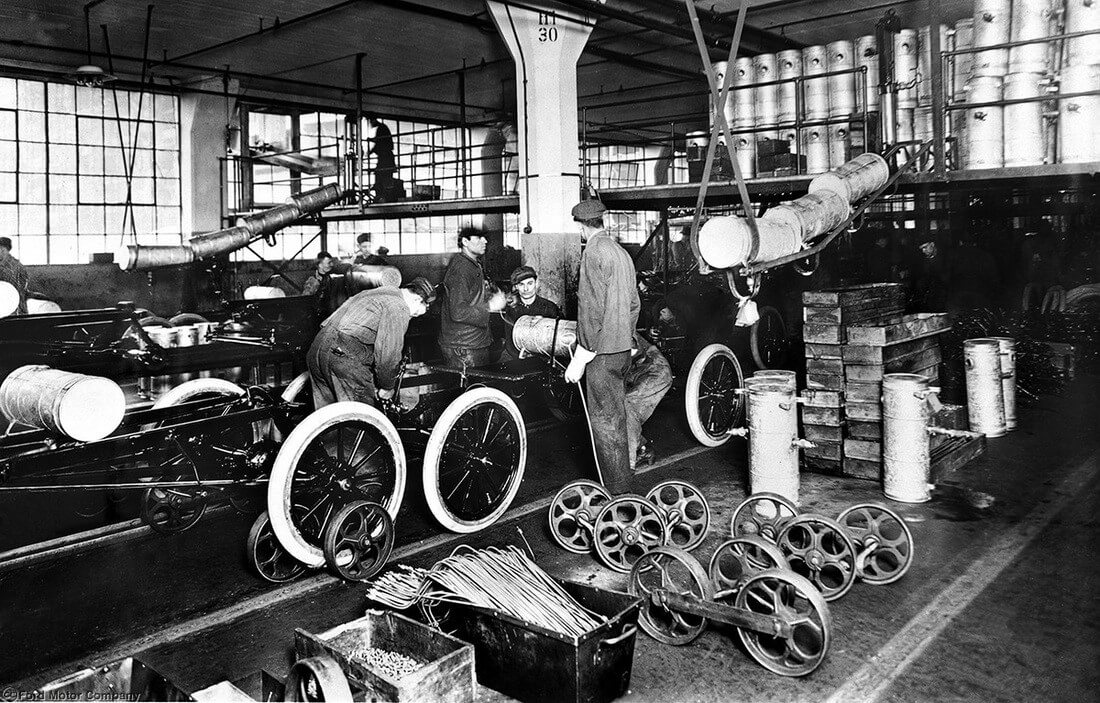
Image source: Industrial Revolution Two
Industry 3.0
Key words: computer and automation
The third industrial revolution started from 1970s when the programmable logic controllers and computers was used to manufacturing. It used IT systems to automate production lines, which has dramatically improved the efficiency and quality of production.
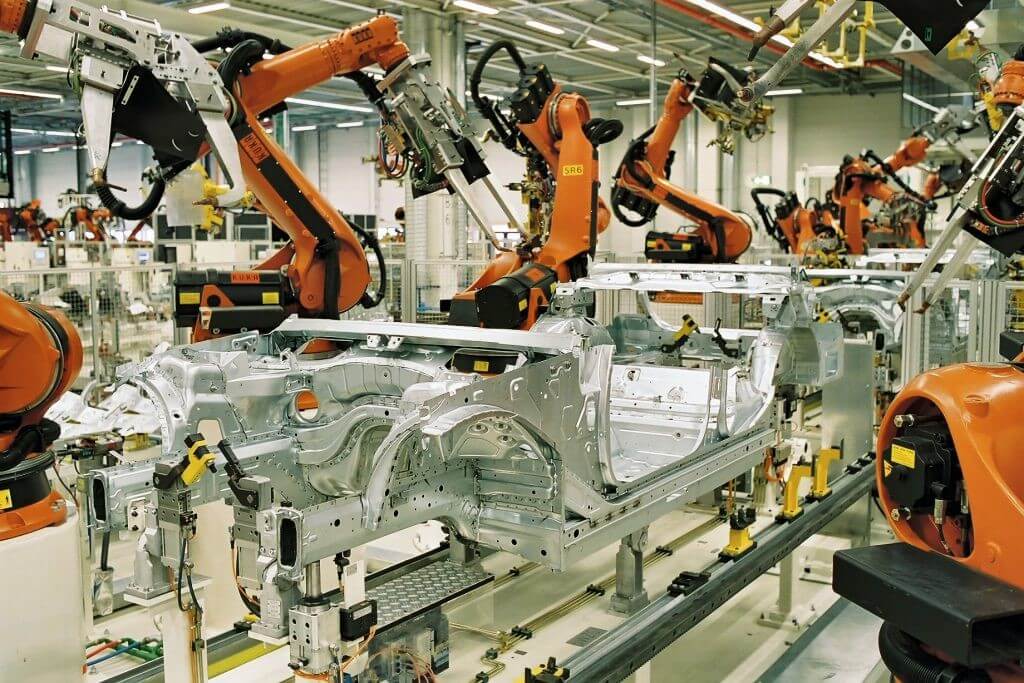
Image source: robotics business review
OK, after a quick overview of last 3 industrial revolution, and let’s go back to Industry 4.0.

So what is Industry 4.0?
Key words: cyber physical systems
The Fourth Industrial Revolution (or Industry 4.0) is the ongoing automation of traditional manufacturing and industrial practices, using modern smart technology. Large-scale machine-to-machine communication (M2M) and the internet of things (IoT) are integrated for increased automation, improved communication and self-monitoring, and production of smart machines that can analyze and diagnose issues without the need for human intervention
Industry 4.0 uses transformative technologies to create a cyber physical system(CPS) for future’s smart manufacturing and smart factories. The transformative technologies include Robotics, AI, big data, IoT, cloud computing, AR, 5G/4G, machine learning, etc. The cyber physical system is now not the individual computerized machines, but the whole network, that have smart machines, intelligent robots, and IoT sensors connected to the network and talk to each other. In this way, the CPS can diagnose their own problems and alert someone that something is going wrong with the machines. Besides, we also have big data technology to use and analyze the data generated by the connected machines. In addition, by using machine learning and AR(artificial intelligence) technologies, we’re able to makes things out of the data, such as predictive maintenance, where a machine or assembly line will tell us it might be going to break down in the next day, so we can fix things before they happen.
5G Empowers Self-driving Forklift In Industry 4.0
Visit below link to learn the case study of how 5G remote-controlled self-driving forklift to improve productivity and safety for industry 4.0
Sources:
1 Comment